Pu Stone Panel Raw Material is a high-density polyurethane rigid foam. This polyurethane structural rigid foam, like ordinary polyurethane rigid foam, is a two-component raw material system. The combined polyacid component (white material) is also mainly composed of polyether polyols with multiple functionalities and high hydroxyl value, and is equipped with catalysts, foaming agents, foam stabilizers, flame retardants and other additives. The isocyanate component is generally crude MDI or crude MDI containing modified MDI. The functionality is more appropriate at about 2.5.
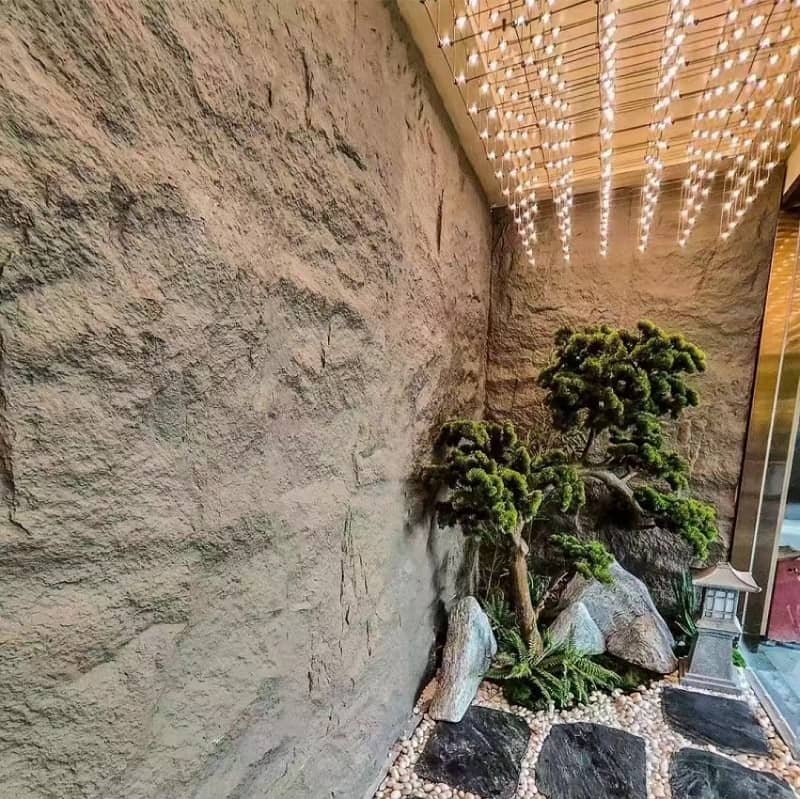
1. Polyether polyol
In the combined polyether premix, polyether polyol is one of the main raw materials. It not only affects parameters such as the viscosity of the combined polyacid and the foaming process, but also affects the physical properties of the product. Generally, within a certain range, the higher the average functionality of the polyether polyol, the greater the crosslinking degree of the prepared polymer, and the higher the mechanical properties and heat resistance of the product. However, high-functionality polyether polyols have high viscosity. The combined polyether has high viscosity and poor process performance such as fluidity of the foaming material, which may cause uneven injection molding and product defects. Therefore, in the raw material system of wood-like rigid foam, generally, some low-viscosity low-functionality polyether polyols (such as polyether diol or polyether triol) are blended in high-functionality polyether polyols. Their proportions are adjusted within a certain range. Mainly high-functionality polyether polyols. The average functionality of polyether polyols can be controlled in the range of 3.5-4 in the world, so that the combined polyether has good fluidity and the rigid foam product has good performance. If the amount of low-functionality polyether is too large, the compressive strength of the prepared rigid foam will be reduced, and the post-curing time of the foam will also increase significantly. Of course, in order to improve the performance decline caused by the addition of low-functionality polyacid and increase hardness, low molecular weight polyols or amine chain extenders can also be added. The addition amount should be controlled below 10%. There are also reports of using a specially prepared single polyether polyol with lower viscosity to prepare polyurethane wood-like materials.
2. Foaming agent
The foaming agents used in the polyurethane foaming process can be divided into two major categories: physical foaming agents and chemical foaming agents. Physical foaming agents are low-boiling-point compounds such as CFC-11, HCFC-141B, and cyclopentane. Chemical foaming agents are generally water. For wood-like items, the thermal conductivity coefficient is not a consideration factor. High-density rigid foam can be prepared by foaming only with water without using physical foaming agents. However, it is also necessary to control the moisture brought in by polyether polyols and others. Excessive water content causes a decrease in product density and strength, and may also cause foam scorching and cracking due to the difficulty in controlling the exothermic reaction of water and isocyanate. And when only water is used as a foaming agent, there are bubbles and holes on the surface of the product. Molded parts do not have an obvious density gradient. The surface strength is low and the practicability is poor. Therefore, the moisture content is generally controlled at a low level, such as about 0.15%, and a low-boiling-point physical foaming agent is added.
The amount of foaming agent (including water) should be adjusted according to the density requirements of the product and whether a dense skin is needed, and determined through mold foaming tests.
The advantages of adding physical foaming agents are to reduce the viscosity of the combined polyacid, improve the fluidity of the foaming material, and adjust and control the density and performance of the foam product. Form a dense skin. The principle of manufacturing self-skinning or integral skin rigid foam is: when molding in a closed mold cavity, the exothermic reaction of the foam causes the material temperature to rise, but the material temperature close to the mold is lower, and the low-boiling-point foaming agent condenses due to the pressure effect, so that there are no bubbles on the skin. The foam plastic close to the skin is also extremely fine and has a high density, thus forming a density gradient from low core density to high skin density. This is particularly important for the production of load-bearing and smooth-surfaced wood-like materials.
CFC-11 is gradually being banned because it damages the ozone layer. Currently, HCFC-141B, cyclopentane and compounded low-boiling-point foaming agents can be used to produce integral skin polyurethane rigid foam imitating wood.
Of course, physical foaming agents can also be omitted in the production of wood-like rigid foam. For example, as introduced in Japanese patents Tokkaihei 8-41154 and Tokkaihei 8-12880, imitation wood polyurethane rigid foam is manufactured by using all-water foaming. For every 100 parts of polyether, 0.8 parts of water is used, and 1 to 50 parts of titanium dioxide or 1 to 10 parts of fine wood powder is used as a filler. The rigid foam product has a good and uniform appearance. Acrylic polyurethane coating can be applied on its surface to obtain wood-like materials. The surface of the rigid foam produced without using filler is not uniform.
3. Catalyst
In the production of polyurethane foam plastics, the selection and addition of catalysts are very important. Choosing different catalyst varieties and quantities can effectively regulate the flow, foaming and gelation processes of materials. Although for high-density rigid foam, the balance of the catalyst in regulating the foaming reaction is not as important as that for low-density rigid tin. However, for the molding production of imitation wood products, catalysts with moderate reaction speed, long cream time and fast curing speed in the later stage should be selected, so that the material has strong flow ability during foaming and can cure quickly after mold filling, with a shorter demolding time and improved production efficiency. Generally, composite delayed amine catalysts are used.
4. Flame retardant
As synthetic wood for furniture, decorations and other products, flame retardants are used to obtain good flame retardant properties. Solid powdered flame retardants have poor compatibility with combined polyethers, which greatly increases the viscosity of materials and has a certain wear effect on high-pressure foaming machine metering pumps, etc., and are less used. Liquid phosphorus-based flame retardants including halogenated phosphate ester flame retardants and other commonly used flame retardants for polyurethane foam can be used. Dimethyl methylphosphonate (DMMP) with a higher phosphorus content has the best flame retardant effect. An addition amount of 4.5% – 5.0% can make the oxygen index reach more than 26. Low-viscosity liquid flame retardants can significantly reduce the viscosity of combined polyacids. But at the same time, it has a plasticizing effect on products. Excessive use not only does not significantly continue to improve the flame retardant performance, but also reduces the hardness and strength of materials. The synergistic effect between different flame retardants can be utilized, and two or more flame retardants can be used in combination. Organic liquid flame retardants and inorganic powder flame retardants can also be used together to reduce costs and enable products to obtain low smoke and high flame retardant properties. Qingdao Lianmei Chemical Company launched flame retardant FR–708 specially for imitation wood furniture and structural foam. It is a colorless low-viscosity liquid. It is said to be particularly suitable for polyurethane high-density imitation wood products and has good compatibility with polyether polyols. It is especially suitable for mold filling of structural composites and carved patterns in furniture. Adding 8–15 parts of FR-708 per 100 parts can meet the requirements of different flame retardant grades. Many halogen-containing flame retardants will slowly hydrolyze in combined polyethers when encountering alkaline amine catalysts, affecting the storage stability of the combined materials. Attention must be paid when using them.
5. Foam stabilizer and other additives
At present, the hard foam stabilizer used is a copolymer of polyether and polysiloxane. There are many product types and grades. Many foam stabilizers can be used in the production of high-density rigid foam. The foam stabilizer not only adjusts the size of the foam pore diameter, but also plays a role of mixing and emulsifying in the pre-mixing process of combined polyether and the foaming reaction, improving the compatibility of combined polyether and isocyanate, making the material more uniform and improving fluidity. It can effectively eliminate the pinhole phenomenon on the foam surface and improve the yield of products. The dosage is generally 1.5% – 2.0%.
Some wood-like products can add color paste to the raw materials, so that the post-coating process of the product can be omitted. And when molding products, if silicone release agent is used, the surface of the finished product needs to be cleaned. The silicone film needs to be removed before coating, which is more troublesome.
In order to prevent aging and discoloration of wood-like materials, anti-aging agents and light stabilizers can be added.
In addition, in order to obtain higher strength, materials such as glass fiber can be used to manufacture reinforced structural foam, so that wood-like products have higher load-bearing performance.

Recent Post
Contact Us
- 86 13590713995
- yan@isopolyol.com
- No.5205, Boyuan Road, Anting Town, Jiading District, Shanghai, China