The following is a simple introduction to the above classifications.
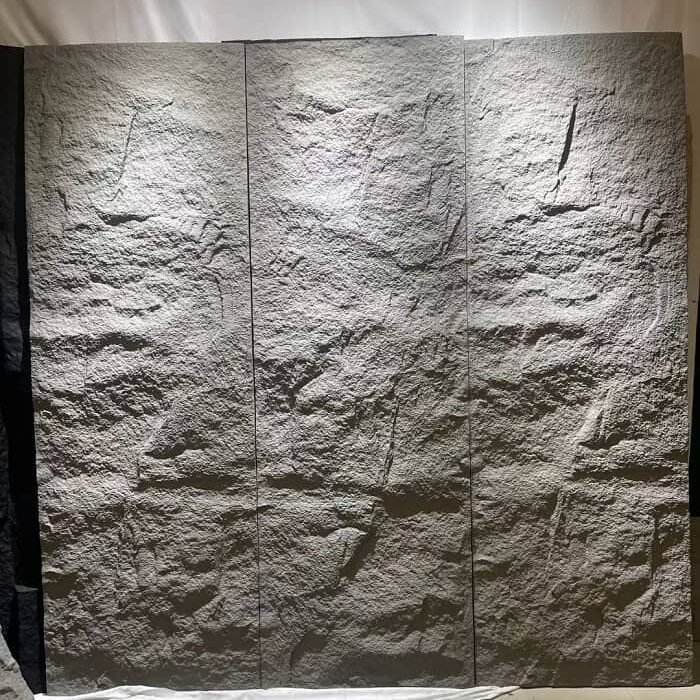
1. Silicone molds
A. Resin soft mold. This is a type with a soft interior and a hard exterior. Inside the mold is a silicone inner mold. The outside is the same as a resin mold. Channel steel plus resin. Insert the silicone mold into the resin outer mold to form a soft interior and a hard exterior. The upper cover of the mold is also a resin mold.
B. Gypsum soft mold. Steel plate plus silicone. First make the silicone mold. Surround it with channel steel as a frame. Then pour in gypsum. Smooth the back. Use two steel plates to make the bottom and cover of the mold respectively. Weld adjustable hinges between the steel plates. Weld lock catches on the other three sides. Turn the silicone mold over and place it flat between the two steel plates. Adjust the hinges and lock catches.
A. When the mold is in production, there is little deformation. The waste edge at the joint with the upper mold is small, and there is not much material leakage. However, the cost will be relatively higher.
B. The upper and lower molds are both steel plates. The hinges are adjustable. The lower mold can be shared. Only the inner mold needs to be replaced. Inner molds of different sizes can be used. But the disadvantage is that both the upper and lower molds are steel plates. The sealing is poor. When the hinges are not adjusted properly, there will be material leakage. And the waste edge at the joint with the upper mold is thicker. The back of the product is not flat and needs to be processed such as grinding and planing the bottom.
2. Resin molds
Resin molds for making wood-like products are not easy to deform. There is almost no difference between the original mold and the finished product. If solid wood with deep and obvious wood grain such as ash is used as the original mold, then after painting the finished product, it can almost be indistinguishable from solid wood. The mold joint line of the product is small. There is also little waste edge from material leakage. The mold change is simple and the size stability is good.
3. Steel molds and aluminum molds
In cases where the order quantity is large and the product pattern is simple and there is no wood grain, this mold can be used for production.
Making steel molds and aluminum molds has a long cycle and high cost. And only products with simple patterns can be made. It also requires professional equipment and professional manufacturers to customize. In cases where there is no long-term stable order, it is not appropriate to open this mold. Moreover, steel and aluminum have fast heat conduction and high temperature. When producing in summer, the mold must be cooled down. Otherwise, there is a possibility of burning the surface.
As can seen from the above, different molds have their own characteristics, advantages, and disadvantages. By mastering these, we can “prescribe the right medicine according to the situation and occasion”, reduce production costs, improve production efficiency, and create more value.

4. Summarize the advantages and disadvantages of various molds for your reference.

Recent Post
Contact Us
- 86 13590713995
- yan@isopolyol.com
- No.5205, Boyuan Road, Anting Town, Jiading District, Shanghai, China