Polyurethane High Resilience Foam
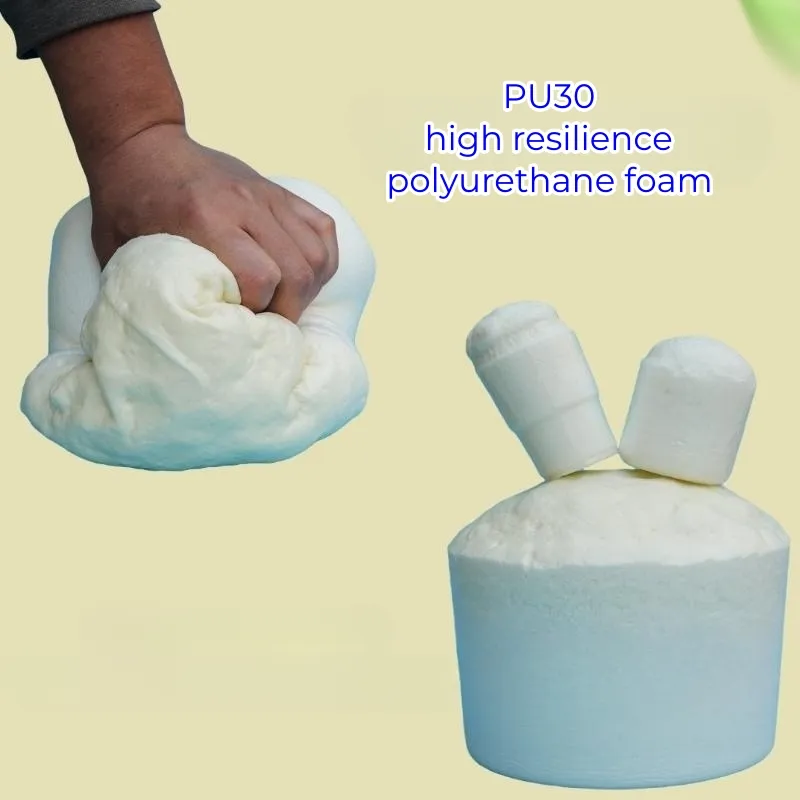
Exploring Polyurethane High-Resilience Foam Applications
Polyurethane high-resilience foam, with its expansive volume, exceptional elasticity, and diverse applications, stands as a testament to the boundless potential of material science. From enhancing automotive seating comfort to revolutionizing furniture and bedding design, this foam continues to shape industries and elevate everyday experiences. Embrace the future of comfort and innovation with polyurethane high-resilience foam.
Polyurethane High-Resilience Foam information
Polyurethane high-resilience foam, a true marvel of material engineering, brings forth a world of possibilities with its remarkable properties and versatile applications. This advanced foam material has garnered attention across industries due to its expansive foaming volume, exceptional elasticity, and suitability for various filling applications. In this comprehensive guide, we delve into the intricate details of polyurethane high-resilience foam, shedding light on its unique attributes, manufacturing process, and diverse applications.
Understanding the Remarkable Expansion
Upon foaming, polyurethane high-resilience foam exhibits an astonishing expansion of approximately 10 to 15 times its original volume. This transformation takes place at a room temperature of 25 ℃, resulting in a voluminous structure that holds immense potential for various industries. For every kilogram of rubber foam, the volume expands to an impressive 12-15 liters, showcasing its high foaming multiplier and exceptional elasticity. This property makes it an ideal candidate for applications requiring softness and enhanced filling capabilities.
The Manufacturing Process: From Mixing to Molding
The manufacturing process of polyurethane high-resilience foam is a delicate dance of chemical reactions and precise timings. The foam’s production begins with a thorough mixing of its two main components: liquid A and liquid B. The recommended weight mixing ratio is 100:40, ensuring the proper balance between the components. However, it’s crucial to note that accurate measurements are vital to achieving the desired material properties and curing outcomes.
Mixing for Optimal Results
Upon measuring the components, it’s important to mix them thoroughly to ensure uniformity. Liquid B is poured into liquid A, and the two are blended using a metal spatula, glass rod, or, ideally, an electric drill. The mixing process lasts approximately 45 seconds, as the chemical reaction between the components initiates the curing process within 1.5 to 2 minutes. Swift and thorough mixing is essential to prevent uneven curing or color deviations in the final product.
Mold Filling and Demolding
After achieving a well-mixed solution, the material is swiftly filled into silicone molds that have been appropriately prepared. It’s crucial to incorporate reserved air holes within the molds to accommodate the gas produced during the reaction, preventing deformation or irregularities in the final foam structure. The filled molds are then set aside for a period of 15 to 25 minutes, during which the curing process takes place. Careful attention is required during demolding, as the heat generated during curing can lead to temperature fluctuations and potential scalding risks.
Applications That Shape Industries
The versatility of polyurethane high-resilience foam is exemplified through its widespread applications across various industries. This foam’s unique combination of elasticity, durability, and expansive volume makes it an essential material for diverse products and purposes.
Automotive Seating Comfort
Within the automotive industry, polyurethane high-resilience foam takes center stage in the creation of comfortable and supportive seating. Its ability to conform to body contours ensures a pleasant driving experience while maintaining its structural integrity over time. The foam’s remarkable elasticity and breathability contribute to enhanced driving comfort.
Furniture Crafting and Soft Packages
In the realm of furniture design, this foam has revolutionized the way we experience comfort. Sofas, chairs, and cushions made with polyurethane high-resilience foam provide unparalleled support and softness, making relaxation a truly luxurious experience. Additionally, the foam’s application extends to leather sculpture soft packages, where its resilience and adaptability create intricate and aesthetically pleasing designs.
Bedding and Restful Sleep
Polyurethane high-resilience foam has transformed the bedding industry by enabling the creation of mattresses and pillows that cater to individual sleep preferences. Its ability to adjust to body shape ensures proper spinal alignment, leading to better sleep quality. The foam’s breathability prevents the accumulation of allergens, contributing to a healthier sleep environment.
Crafting and Toys
The foam’s versatility transcends practical applications and extends into the realm of creativity. Crafters and toy manufacturers alike benefit from its elasticity and ease of manipulation. The foam’s uniform and dense bubble holes provide a consistent texture, making it an ideal medium for crafting intricate designs and durable toys.
Industrial Sound Absorption
In industrial settings, polyurethane high-resilience foam plays a significant role in sound absorption and noise reduction. Its open-cell structure effectively dampens sound waves, contributing to quieter and more controlled work environments. This application is particularly valuable in spaces such as recording studios and manufacturing facilities.
Considerations for Optimal Results
To harness the full potential of polyurethane high-resilience foam, certain considerations should be kept in mind:
Temperature Control: Both the material and mold temperatures significantly impact the foam’s properties. Maintaining A and B components at around 25℃ during production ensures optimal processing and molding conditions.
Air Exposure and Clumping: The B material is prone to clumping upon exposure to air. Prompt usage is recommended to prevent unwanted clumping and ensure the foam’s consistency.
Color Customization: Color paste or later spray paint can be added to achieve desired hues in the final foam products.
Mold Release Agent: Applying a mold release agent to the mold surface enhances the demolding process, promoting easy release of the finished product.
Polyurethane high-resilience foam, with its expansive volume, exceptional elasticity, and diverse applications, stands as a testament to the boundless potential of material science. From enhancing automotive seating comfort to revolutionizing furniture and bedding design, this foam continues to shape industries and elevate everyday experiences. Embrace the future of comfort and innovation with polyurethane high-resilience foam.
Polyurethane High-Resilience Foam
Applications
Construction Videos
FAQ
Polyurethane high-resilience foam has garnered widespread attention for its exceptional properties and versatile applications. As you delve into the world of this remarkable foam, you may have questions about its characteristics, usage, and benefits. In this FAQ guide, we address some of the most common queries to provide you with a comprehensive understanding of polyurethane high-resilience foam.