What is High-density Polyurethane Imitation Wood?
High-quality high-density polyurethane imitation wood materials offer exceptional durability and design flexibility, standing as an advanced alternative to conventional wood and veneer furniture. Traditional solid wood furniture may look great, but it eventually wears out and needs replacement. Veneer furniture, often made from medium-density fiberboard (MDF) using wood and plant fibers bonded with adhesive, is limited in design—its rigid form restricts intricate shapes and curves. Plus, MDF generally falls short on environmental, moisture, and durability fronts.
On the other hand, high-density polyurethane wood alternatives are a standout choice. Not only do they allow for intricate shapes and mold designs without the need for carving, saving on production costs, but they also provide the toughness of solid wood without drawbacks like cracking or insect vulnerability. This durable, insect-resistant, and moisture-proof material supports longevity for a range of applications.
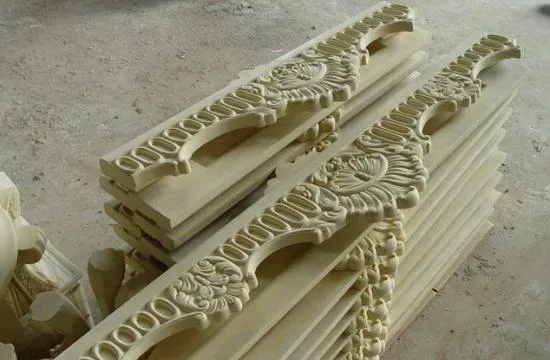
What is High-density Polyurethane Imitation Wood?
Polyurethane imitation wood, made from high-density polyurethane rigid foam, has a micro-pore structure. Compared to standard insulation foam, it has a much higher density (typically over 200kg/m³). This dense material delivers wood-like qualities—strength, scratch resistance, and an appearance close to real wood. Additionally, with a lower-density core, products made from this material remain lightweight yet maintain exceptional strength in compression, tension, impact, and bending.
This synthetic wood alternative has closed-cell pores, making it resistant to moisture absorption. Studies show that high-density polyurethane rigid foam absorbs significantly less water than traditional wood, which helps retain its strength over time, even in damp environments.
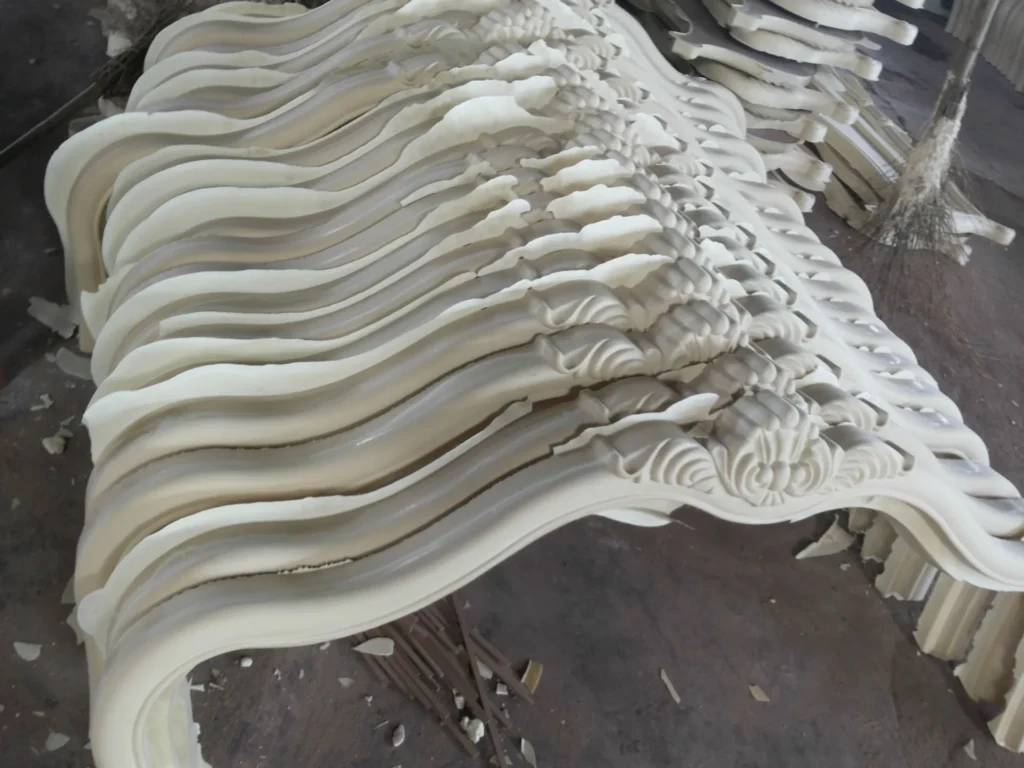
Production of high-density Polyurethane Imitation Wood
Polyurethane imitation wood is crafted from medium-to-high density rigid foam through processes like blending, foaming, and injection molding. This two-part raw material system includes a polyether component (white material) and a polyisocyanate component (black material). Once processed, it forms a sturdy, wood-like material often called “PU imitation wood.”
Typical production involves:
- Determining Formula: Calculating the material amounts to get desired density and volume.
- Preparing the Mold: Cleaning, applying release agents, and placing embedded support parts.
- Mixing and Pouring: Mixing raw materials and pouring them into the mold.
- Rotating and Curing: Ensuring even coating and allowing the material to cure.
- Finishing: Removing flash, performing final sanding, and adding paint for a polished look.
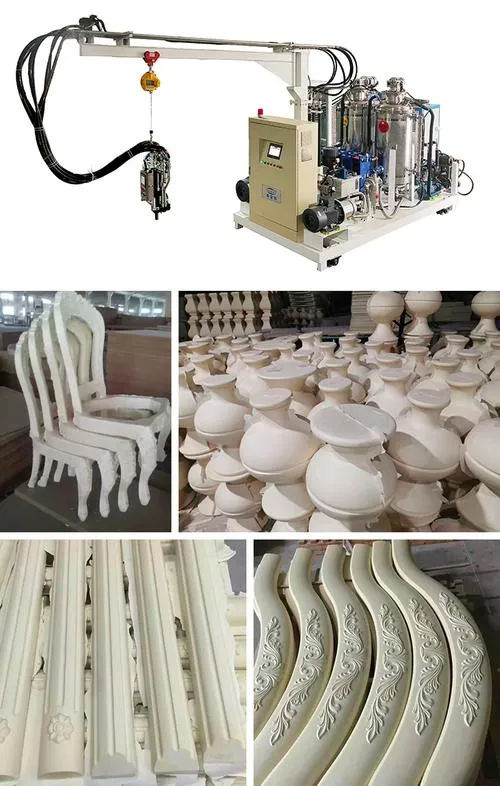
Performance and Benefits of Polyurethane Imitation Wood
Polyurethane imitation wood stands out for its easy, cost-effective production, allowing large-scale industrial manufacturing. It can be molded into complex patterns and intricate shapes with wood-like textures and fine details. Lightweight yet strong, it resists impact, corrosion, insects, and even extreme temperatures (-50°C to 70°C), with a service life that can reach 14 years if kept undamaged. The addition of flame retardants can make high-density polyurethane materials safer than natural wood for certain applications.
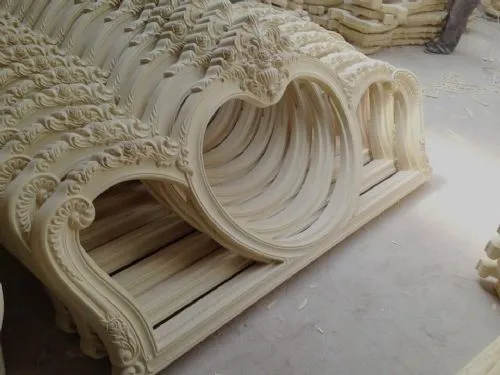
Comparing Polyurethane Imitation Wood with Natural Wood
High-density polyurethane imitation wood holds up impressively well in strength-to-weight ratios compared to other synthetic materials like ABS and PET. While natural wood has superior mechanical strength, polyurethane imitation wood delivers enhanced surface hardness, superior moisture resistance, and the ability to create complex, decorative designs. This makes it a versatile choice for furniture and design elements that don’t rely solely on structural support, yet require high durability and an authentic wood look.

Recent Post
Contact Us
- 86 13590713995
- yan@isopolyol.com
- No.5205, Boyuan Road, Anting Town, Jiading District, Shanghai, China