In the world of coatings and sealants, technological advancements have introduced various innovative solutions to protect and enhance surfaces. One such breakthrough is the polyaspartic coating, which has gained popularity for its exceptional performance and durability in a wide range of applications.
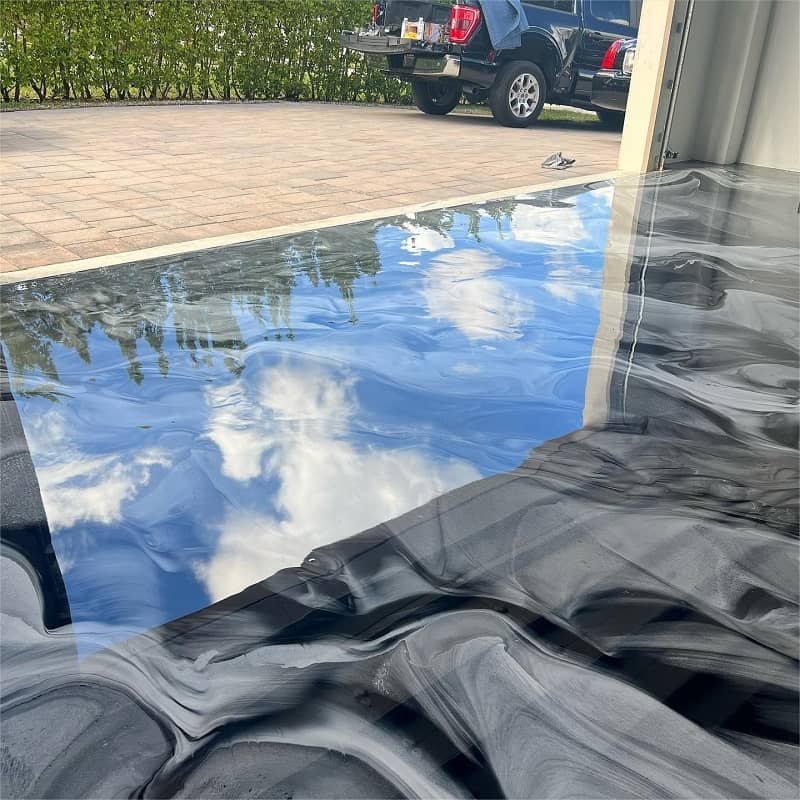
Pure Polyaspartic Coating
1. Polyaspartic Coating Material Ratio and Usage:
Polyaspartic is a two-component system. During construction, pour the two containers of materials, AB, into a container in a one-to-one ratio by weight and stir for 2-3 minutes before application. The mixed material should be used within 50 minutes. (Note: If the set of materials is used multiple times, it must be weighed and proportioned using an electronic scale.) Construction requires a clean and dry substrate, no application on wet surfaces!
(1) Substrates Suitable for Polyaspartic:
Cement surfaces, ceramic tile surfaces, wood, sunroom glass, canvas, microcement, floorings, marble, glazed tiles, and true stone paints.
① Polyaspartic can be applied on water-based coatings.
② After Polyaspartic forms a film, it can be painted on with oil-based or water-based coatings and paints.
③ Polyaspartic can be applied on polyurethane coatings.
④ Polyaspartic cannot be applied on asphalt and roll materials (the asphalt and roll materials must be completely removed before using polyaspartic).
(2) Diluent Addition:
Add 10-20% of the total volume of diluents such as xylene, butyl acetate, ethyl acetate, or esters with a water content of less than 0.05%, as per personal requirements.
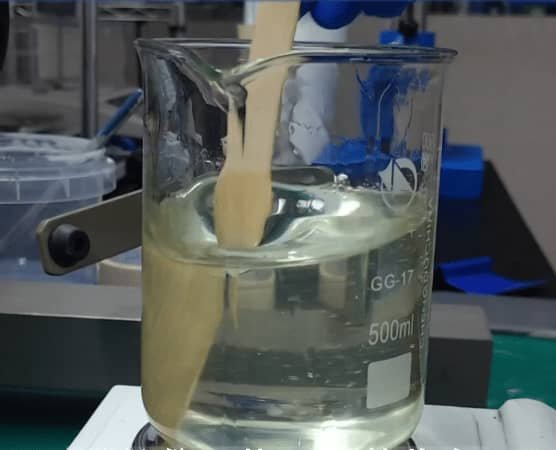
2. Polyaspartic Application Techniques on Various Substrates:
(1) Cement-Based Surface Construction Process:
For aged and weathered surfaces older than 20 years, ensure they are clean and dry before construction:
① For the first application, mix components A and B in a one-to-one ratio by weight, and apply 20% of the total Polyaspartic with diluent on large surfaces during the first coat.
② After 2 hours, apply the second coat when the first coat is dry. Mix Polyaspartic thoroughly and apply directly. After 72 hours, a water test can be performed.

(2) True Stone Paint Application Technique:
① Clean the substrate from dust and ensure it is dry.
② Mix components A and B in a 1:1 ratio as per the formula, and apply by rolling, brushing, or high-pressure airless spraying for 1-2 coats.
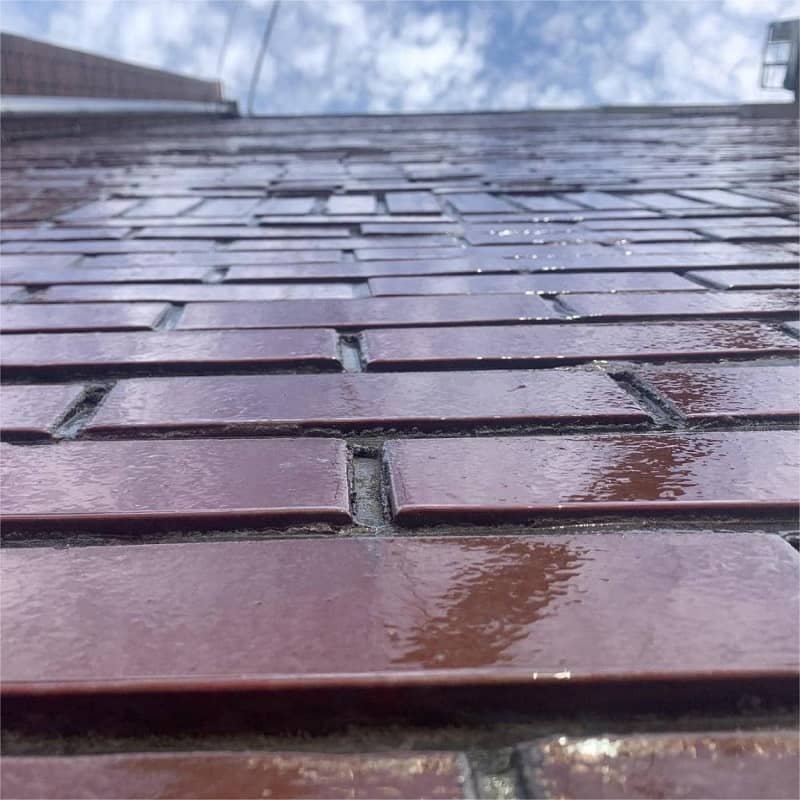
(3) Exterior Wall Tile Surface Construction Process:
① Treat the grouting and ensure the substrate is clean and dry.
② Apply 1-2 coats of Polyaspartic by brushing or spraying.
③ For tile surface refurbishment and color change (ISO&POLYOL pigment outdoor resistant to aging at level 7-8 and high temperature of 200 degrees Celsius), add ISO&POLYOL pigment to white Polyaspartic paint for DIY and create desired colors.
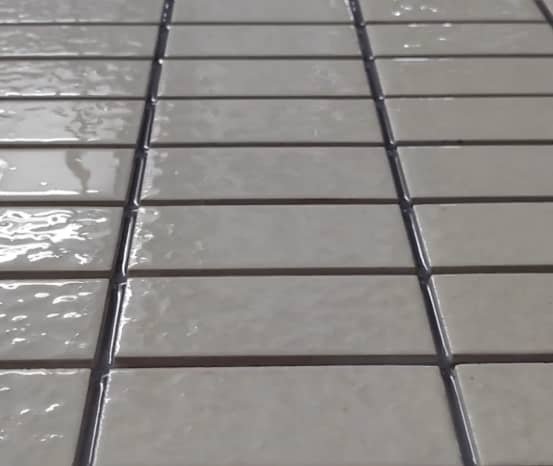
(4) Concrete-Based New Kitchen/Bathroom Waterproofing:
① Clean and keep the substrate clean and dry.
② For the first application, add 20% diluent to the total amount of Polyaspartic and mix it well. Apply a thin coat of Polyaspartic (the diluent is added to enhance the low viscosity of Polyaspartic, making it easy to penetrate into the concrete).
③ After 3 hours, when the surface is not sticky, apply the second coat of Polyaspartic. After 72 hours, a water test can be performed.
(5) Industrial Wear-resistant/Anti-slip/Protective Floor Process (Concrete-based):
① A: Grind and clean the substrate, keep it clean and dry. First, apply a 20% dilution of Polyaspartic in the first step.
② Apply the second coat (determine the amount based on thickness). ISO&POLYOL Polyaspartic film’s hardness after curing is Shao’s hardness D-55-65 (contact customer service for customized formulas with different hardness levels). B: Polyaspartic can be directly applied on epoxy floor or self-leveling surfaces for anti-slip, anti-corrosion, and protective purposes.
(6) Glass Surface Construction Process:
① Clean and dry the surface.
② Apply (ISO&POLYOL special primer) and wait for 3-5 hours for it to dry.
③ Begin the Polyaspartic application with 1-2 coats.
(7) Metal Surface Waterproofing/Anti-corrosion/Protection Application Process:
① If there is rust, grind it clean and dry.
② Apply zinc-rich or ISO&POLYOL primer as the base coating.
③ Apply Polyaspartic coating (the thickness depends on the application).
3. Performance Indicators:
Tensile strength and elongation at break: Polyaspartic achieves tensile elongation of 400% and tensile strength of 69 MPa, tear strength of 129 kgf/mm according to GB/T16777-2008 standard when a transparent pure Polyaspartic film with a thickness of 1.0 mm is tested on the tension test machine. The film exhibits excellent performance in various applications such as anti-seismic, thermal expansion and contraction resistance, and long-term protection for bridges, concrete, and tiles.
Artificial climate accelerated UV aging performance: According to GB/T14552-2008 standard, ISO&POLYOL Polyaspartic was tested with a 1.0 mm film thickness, subjected to 4000 hours of UV accelerated aging in a simulated environment. The results show that ISO&POLYOL Polyaspartic film does not fade, powder, crack, peel, wrinkle, bubble, or become brittle after exposure to controlled high-temperature UV light, providing a reliable basis for metal corrosion protection, outdoor flooring, and concrete waterproofing and protection applications.
Salt spray corrosion resistance performance: According to GB/T31588.1-2015 standard, ISO&POLYOL Polyaspartic was tested in a simulated marine environment with a 5% sodium chloride standard solution as the spray solution. After 3000 hours of cyclic spray experiment under 36 degrees with saturated air, the Polyaspartic film shows excellent resistance to chloride ion salt spray corrosion. It does not bubble, change color, powder, rust, crack, or peel, ensuring a theoretical service life of more than 20 years for applications on metal surfaces or ship anti-corrosion and concrete structures.
Impact resistance performance: According to GB/T 1732-2020 standard, ISO&POLYOL Polyaspartic was tested with a 1 kg, 100 cm heavy hammer falling on the pre-coated test plate. The Polyaspartic film shows no fractures, damage, cracks, peeling, or fragmentation, demonstrating excellent impact resistance.
High and low-temperature resistance: ISO&POLYOL Polyaspartic can be used continuously at 120 degrees Celsius without delamination from the substrate. It can withstand temperatures up to 350 degrees Celsius. It also has excellent low-temperature resistance down to -65 degrees Celsius without hardening or cracking.
Adhesion performance: ISO&POLYOL Polyaspartic exhibits strong adhesion with tiles, cement, glass, and steel structures, achieving an adhesion strength of over 10 megapascals.
Heat insulation performance: Polyaspartic (non-radiation heat insulation) in gray, white, green, blue, yellow, and black colors can lower temperatures by 24 degrees Celsius at 69 degrees Celsius (insulation principle). Polyaspartic relies on its film density for heat insulation, with a density 40 times higher than ordinary coatings.
Anti-slip and wear-resistant performance: Polyaspartic film has a certain flexibility and strength, with a hardness of 45D, allowing it to withstand long-term foot traffic and vehicular loads. It becomes highly slip-resistant when exposed to water.

Recent Post
Contact Us
- 86 13590713995
- yan@isopolyol.com
- No. 2, Chun Hai Road, Chengyang District, Qingdao, Shandong - China